Tribological Behavior of Electrochemically Phosphated Pearlitic Rail Steel
Collaboration: Empa
Responsible: Mohammad Alinezhadfar
Project: Metrohm Stiftung (Metrohm Foundation) PhD project
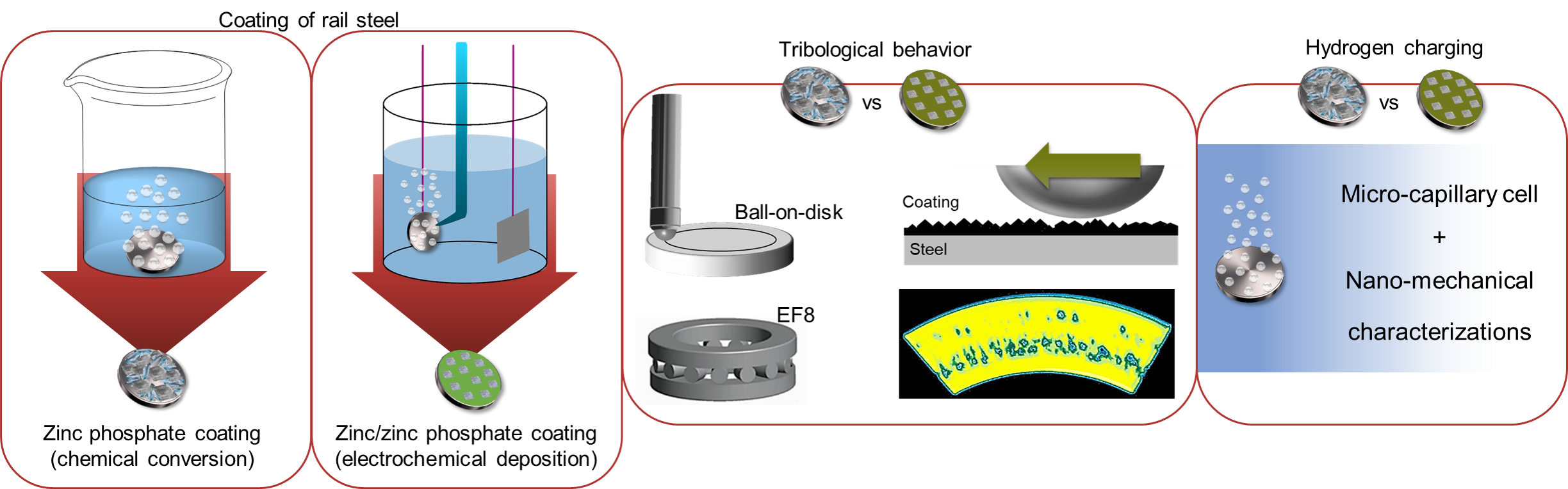
Background
The wheel-rail interface is complex and prone to safety problems, such as flange climbing, material breakage, and wheel and rail fracture. Lubricants and conditioners are often used to partially control wear, rolling contact fatigue (RCF), vehicle performance, energy efficiency, and noise. Wear and RCF are major concerns in wheel-rail contact, and various methods have been used to address these issues, including coatings and surface modification of rail steel. A low-cost deposition of a durable and lubricating coating that can protect the rail system against wear, fatigue, and corrosion may be a solution to these problems.
Phosphate coatings, particularly zinc phosphate coatings, are frequently used for lubrication and corrosion protection purposes. Nevertheless, the traditional deposition method through chemical conversion can decrease efficiency due to the formation of sludge during the coating process. Additionally, the high operating temperatures required for phosphating baths exacerbate the problem. To overcome these challenges, electrochemical acceleration has been developed as an effective method for depositing thick zinc phosphate coatings with minimal porosity at lower temperatures. This technique allows for the re-deposition of coatings in damaged areas and offers a controlled and accelerated process for coating deposition. The electrochemical method of depositing zinc phosphate leads to the formation of different types of coatings as metallic zinc is created during the process, resulting in a composite of zinc and zinc phosphate. While some studies have explored the corrosion behavior of these composites, further research is needed to fully understand their formation mechanisms and tribological/mechanical properties.
Aim and objectives
To develop a low-cost deposition process for a durable coating that protects against wear, fatigue, and corrosion, this project aims to develop novel zinc phosphate coatings suitable for tribological and heavy-duty applications. The goal is to target the formation mechanism of these coatings using novel characterization techniques. In order to achieve this, formation of zinc phosphate conversion coatings on pearlitic rail steel, electrochemical deposition of zinc / zinc phosphate composites, tribological performance of conversion and electrochemical composite coatings, and hydrogen embrittlement of the substrate will be investigated in this project.
Methodology
This research aims to coat pearlitic rail steel with high manganese content with zinc phosphate through both chemical conversion and electrochemical deposition methods. In the case of chemical conversion coating, the study will focus on the effect of pH, temperature, and substrate type on the phase structure, composition, and mechanical/tribological properties of the coatings. By determining the coating formation mechanism, deposition of zinc phosphate conversion coatings will be optimized with respect to its tribological behavior. Similarly, electrochemical deposition of zinc/zinc phosphate coatings will be carried out using different applied potentials, current densities, bath pH, and counter electrode types. The composition and structure of the coatings will be determined, and the formation mechanism will be studied using potentiostatic, galvanostatic, and pulsed cyclic potentiostatic/galvanostatic methods.
The optimized zinc phosphate conversion and electrochemical coatings will be evaluated in terms of their tribological performance, including friction response and fatigue behavior using ball-on-disk and a modified FE8 tests. Wear track cross-sectional analysis will be performed to evaluate the chemical changes in the coating and damage induced to the substrate. Additionally, the amount of hydrogen charging during each deposition method will be characterized using microcapillary cell electrochemical method and nano-mechanical characterizations.